
Process Combustion Corporation's Flameless Thermal Oxidizer (FTO) systems are the best solution for applications that require the highest Destruction Removal Efficiencies (DRE) and lowest NOx emissions. Each FTO is fully automated and engineered to accept the full range of waste gas compositions and flow rates generated by our customer's manufacturing process.
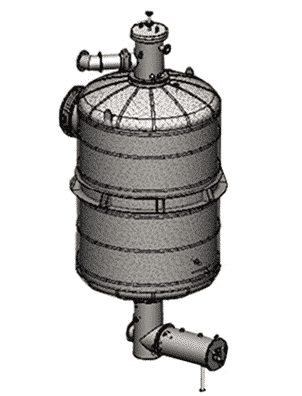
Untouchable DRE > 99.9999%
Ultra Low NOx < 1 ppmv
Self-sustaining for Waste Gas > 10 BTU/scf
100% Waste Gas Turndown Capability
How do we achieve such low NOx?
A typical burner system can have hot spots within its flame that exceeds 3000°F. High flame temperatures, even for short residence times (msec), can generate large amounts of Thermal NOx.
PCC's Flameless Thermal Oxidizer premixes waste gas with air and natural gas prior to treatment. The FTO's operating temperature is lower and more uniform throughout the media bed which leads to NOx generation as low as 1 ppmv.
Managing Change - Efficient management of waste stream
50% less Thermal NOx
In a global economy with a number of potential control technologies to choose from, it is important for companies to understand their options.
.
Flameless Thermal Oxidizers FAQ
Flameless oxidation is a thermal treatment that premixes waste gas, ambient air, and auxiliary fuel prior to passing the gaseous mixture through a preheated inert ceramic media bed. Through the transfer of heat from the media to the gaseous mixture, the organic compounds in the gas are oxidized to innocuous by-products, i.e., carbon dioxide (CO2) and water vapor (H2) while also releasing heat into the ceramic media bed. PCC’s Flameless Thermal Oxidizers are designed to operate safely and reliably below the composite LFL while also maintaining a constant system flow and temperature. Waste gas streams experience multiple seconds of residence time at high temperatures leading to measured destruction removal efficiencies that exceed 99.9999%. Premixing all of the gases prior to treatment eliminates localized high temperatures which leads to thermal NOx as low as 1 ppmv.
In a global economy with a number of potential control technologies to choose from, it is important for companies to understand their options. It is also important to recognize that environmental regulations can only get more stringent in the future. Forward-thinking companies with a strong sense of corporate social responsibility want the best available control technology (BACT) at their manufacturing facilities. Flameless Oxidation has proven to be the best control technology for the Pharmaceutical and Specialty Chemical Industries.
PCC offers two different types of Flameless Thermal Oxidizer models based on the volume of waste gas being treated:
Model | Treatment Capacity (scfm) |
Electric FTO | 0 to 100 |
Elliptical FTO | 750 to 100,000+ |
Electric FTO
- The electric model consists of a vertical refractory lined vessel filled with ceramic media.
- Ceramic media is preheated through the use of electric resistance heaters.
- Waste gas and ambient air are premixed at the bottom of the unit and introduced into the unit.
- Organic compounds in waste gas are oxidized and discharged to atmosphere via a stack extension on the top of the vessel.
Elliptical FTO
- The Elliptical model is a refractory lined cylinder partially filled with ceramic media.
- Ceramic media is preheated through the use of an auxiliary natural gas burner.
- Waste gas, ambient air, and natural gas are premixed at the top of the vessel and delivered to media bed through use of a central dip-pipe.
- Heat is generated via the oxidation of natural gas and waste gas.
- Destruction Removal Efficiencies up to 99.9999%.
- Thermal NOx emissions of less than 1 ppmv.
- Self-sustaining for fume streams as low as 10 BTU/scf
- Ceramic media bed is stable and resilient to temperature fluctuations.
- Sets the bar for BACT requirements for gaseous waste streams.
- Waste stream feed forward control ensures stability and prevents nuisance shutdowns.
A typical burner system can have hot spots within its flame that exceeds 3000°F. High flame temperatures, even for short residence times (msec), can generate large amounts of Thermal NOx.
PCC's Flameless Thermal Oxidizer premixes waste gas with air and natural gas prior to treatment. The FTO's operating temperature is lower and more uniform throughout the media bed which leads to NOx generation as low as 1 ppmv.
In any Oxidation System, destruction is determined by the Three T's:
- Time: Residence Time
- Temperature: >1400°F
- Turbulence: Efficient or Premixing
PCC's Flameless Thermal Oxidizer achieves all three of these critical factors, by design.
Time
The flow through a PCC Flameless Thermal Oxidizer involves multiple seconds of residence time at high temperatures. Because perfect mixing has already been achieved, high gas velocities are not required. As a result, the flow through each unit can be slower leading to longer retention times for oxidation reactions to reach completion.
Temperature
Each PCC Flameless Thermal Oxidizer operates with a completely uniform temperature profile that means the entire gas flow passes through a bed with a constant temperature profile to ensure that optimum destruction is achieved.
Turbulence
A PCC Flameless Thermal Oxidizer perfectly mixes waste gas, air, and fuel gas. This allows excess oxygen to more successfully find and react with organic material in the gas mixture once preheated to each compounds auto-ignition temperature.